The Sustainable Promise of a Wood-Plastic Composite
Wondering how to make a product sustainable? Wood-plastic composites combine qualities uniquely suited to accommodating both consumer and producer preferences in the current market. They are a sustainable solution that makes use of organic material with virgin, recycled or renewable plastics. They can be customized at low cost and without the need for investment in new production equipment. The result is a cost-competitive product that offers a lighter environmental footprint, unique aesthetic appeal and superior performance.
A sustainable direction
Manufacturers have been combining petroleum-based plastics with organic material since the very early days of plastics manufacturing. Rice hulls, walnut shells and ground oyster shells were all used as affordable fillers that enabled manufacturers to cut costs while maintaining quality. Eventually, inorganic materials, such as chalk and calcium carbonate were substituted with the goal of making a more affordable plastic.
But there were downsides to using inorganic fillers. As more and more were added to the plastic, the finished product lost impact strength and became too rigid. For a time, adding filler to plastic was seen as a weakness and a mark of inferior quality.
Eventually, the focus began to shift from using inorganic fillers to again using organic material to supplement plastic production. Wood was introduced. Using sawdust and other waste materials from sawmills proved to be an affordable and sustainable tactic for making a plastic that was not only of high quality, but also visually appealing to consumers. Wood pulp added a renewable material to the process, reducing dependency on petroleum-based raw materials.
Wood-plastic composites feature the benefit of reduced melting temperature, resulting in lower energy costs for producers, and further reducing the product’s environmental impact. Wood-plastic composites may often be used with existing tooling. For manufacturers, this eliminates an investment that would need to be recouped before cost savings could be realized. And since wood does not need to be treated when making wood-plastic composites, wood scrap could be used immediately after being reclaimed, without the addition of potentially harmful chemicals.
Today, the classic look of wood can be effectively imitated, but with the added benefits of improved strength, durability, and weatherability. As entrepreneurs and sustainability-minded businesses continue to enter the market, wood-plastic composites are emerging as a solution for a wide variety of consumer product applications.
For more on how to make a product sustainable, download our white paper on the benefits of wood-plastic composites.
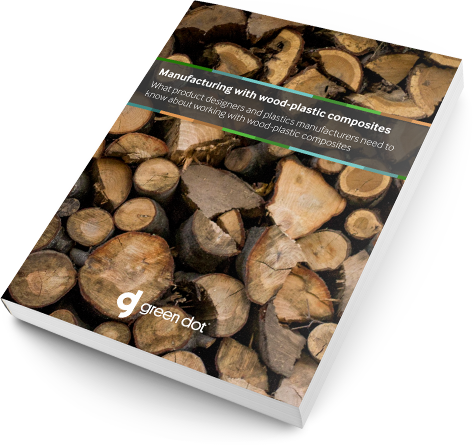
Working with wood-plastic composites
Why plastics manufacturers have nothing to fear by switching to a wood-plastic composite alternative material